What is a HOWFIT knuckle type high speed precision punch
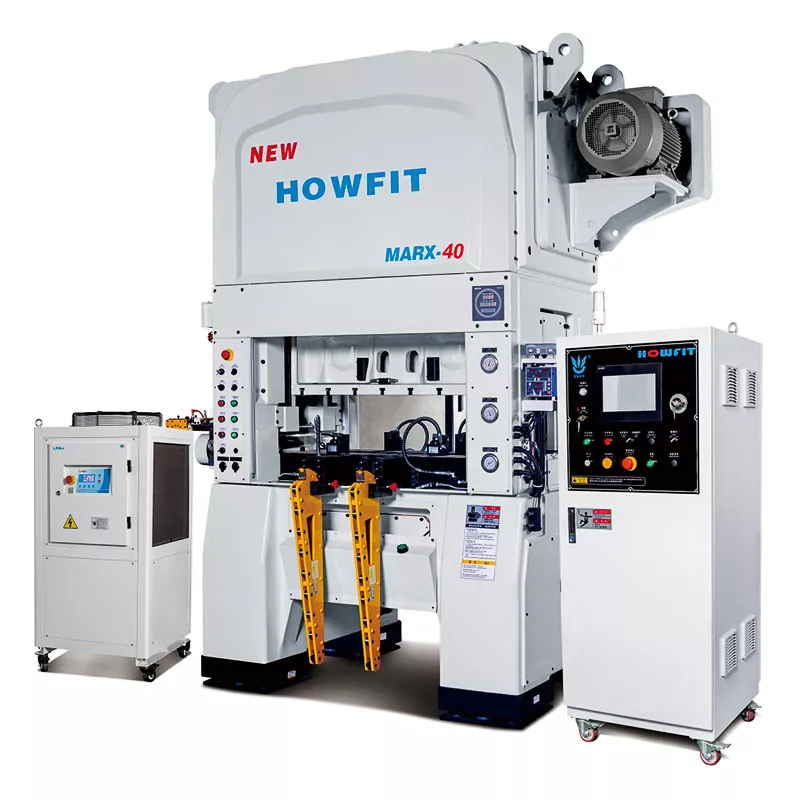
Certainly! Here's a simplified version of the first part of your text about the working principle of
a HOWFIT toggle-type high-speed precision press
**Part 1: Working Principle of a Toggle-Type High-Speed Precision Press**
Stamping technology plays a crucial role in modern manufacturing, making production processes more efficient, precise, and controllable. In this context, toggle-type high-speed precision presses have become widely used, and their engineering principles and applications are gaining attention.
**1. Basic Structure and Components of the Press**
A toggle-type high-speed precision press is a specialized machine typically consisting of several key components. One of the most important components is the machine base, which provides stability and mechanical support for the press. Mounted on the base is a slide, which is the primary working part of the press. The slide moves vertically and performs the stamping operation.
Another critical component is the die, which is positioned beneath the slide. The shape and size of the die determine the final product's shape and dimensions. When the material is placed between the die and the slide, and the slide applies downward pressure, the material is cut, punched, or bent to create the desired parts.
**2. Working Cycle and Stamping Process**
The working cycle of a toggle-type high-speed precision press is a highly automated and repetitive process. Typically, a workpiece or material is loaded into the working area manually or automatically. Then, the press is activated by the control system. Once initiated, the slide descends rapidly, and the die comes into contact with the workpiece, initiating the stamping process. This process generally involves four main stages:
- **Downstroke Phase:** The slide descends and makes contact with the workpiece, applying pressure.
- **Stamping Phase:** In this phase, the press applies sufficient force to cut, punch, or bend the workpiece. This is a critical stage for producing the parts.
- **Upstroke Phase:** The slide ascends, separating the workpiece and the die, allowing the finished product to be removed or further processed.
- **Return Phase:** The slide returns to its initial position, preparing for the next stamping operation.
**3. Automatic Control and Monitoring Systems**
Modern toggle-type high-speed precision presses are usually equipped with advanced automatic control and monitoring systems. These systems ensure a high level of precision and repeatability in the work. The control system can adjust press parameters such as downstroke force, descent speed, and the number of stamping cycles to meet the requirements of various workpieces.
Simultaneously, monitoring systems track key parameters like pressure, displacement, and temperature in real-time to ensure the stability of the stamping process. If any irregularities are detected, the system can take immediate action to prevent product quality issues or equipment failures.
Through these automatic control and monitoring systems, toggle-type high-speed precision presses achieve high levels of accuracy and control while enhancing production efficiency.
In the upcoming parts of this article, we will delve into the engineering design and advantages of toggle-type high-speed precision presses, their applications in various industries, and explore the future development trends in press technology and the importance of engineering in the manufacturing industry. We hope this article will help readers gain a deeper understanding of this crucial manufacturing technology.
With years of hands-on experience, I have honed my skills in navigating the complexities of global commerce, offering invaluable insights and solutions to address customer needs. My commitment to excellence and dedication to customer satisfaction ensure that I deliver exceptional service, guiding clients through every step of the trading process with confidence and proficiency.