400-ton high-speed precision punch machine in the new energy automobile industry
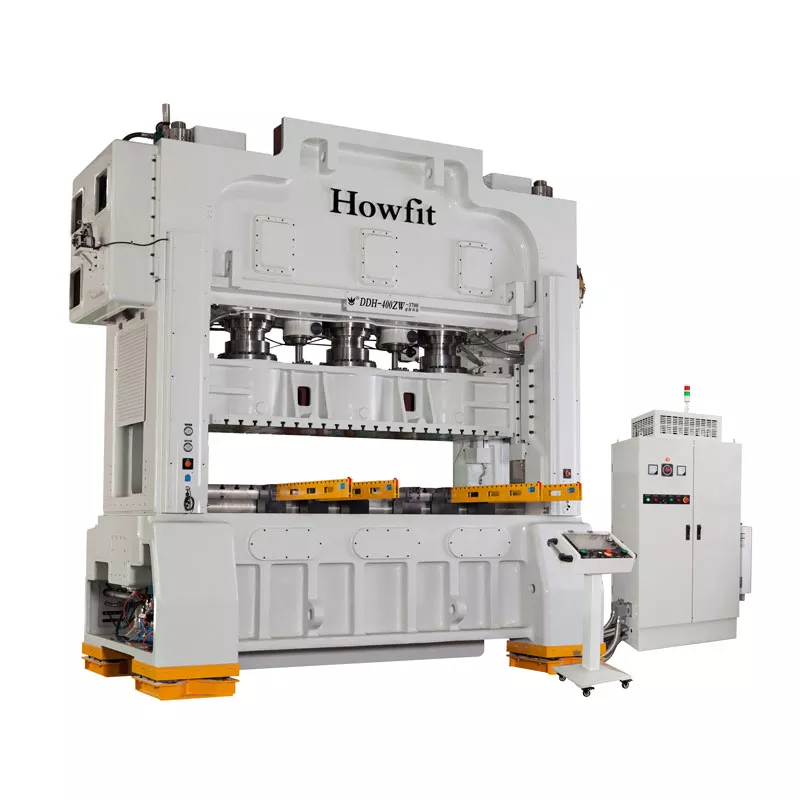
1. Key features and advantages of DDH-400ZW punch press
Ultra-wide workbench and adaptability to multiple complex processing techniques:
The DDH-400ZW punch press has a worktable with a maximum width of 3700mm, which can adapt to more complex processing technology requirements. This provides a broader application space for the stamping processing of complex motor stators and rotors in the new energy automobile industry.
Stable bottom dead center repeatability and extended mold life:
The stable bottom dead center repeatability of the punch can reduce mold wear, ensure product accuracy while reducing bottom dead center runout, and extend the service life of the mold. This is crucial to saving costs and improving production efficiency.
Minimizing thermal displacement and improving processing accuracy:
DDH-400ZW punch press adopts advanced thermal control technology to suppress thermal displacement to the greatest extent and improve product processing accuracy. This is of great significance for the production of precision parts such as motor stators and rotors.
High-precision 8-sided slider guide rail and improved stability:
The punch machine adopts eight-sided slide rails and needle roller slide rails, which have the characteristics of ultra-high bearing capacity and resistance to eccentric load. The long life and convenient maintenance of the guide rails ensure continued and efficient production.
2. The impact and application cases of DDH-400ZW punch press in the new energy automobile industry
Improve production efficiency: Through the high-speed and high-precision characteristics of the DDH-400ZW punch press, new energy vehicle manufacturers can greatly increase the stamping processing speed of motor stators and rotors, thus speeding up the production pace and improving production efficiency.
Improve product quality: The stable repetition accuracy and thermal displacement minimization characteristics of the DDH-400ZW punch machine can ensure that the machining accuracy of the motor stator and rotor reaches a higher level and improve product quality.
Increase production flexibility: The advantages of the DDH-400ZW punch press in terms of workbench width and adaptability to multiple complex processes enable new energy vehicle manufacturing companies to produce more diversified and personalized motor stators and rotors, enhancing production flexibility.
Reduce production costs: By reducing mold wear, extending mold service life and reducing scrap rates, the DDH-400ZW punch helps companies reduce production costs and improve production efficiency.
Strengthen market competitiveness: With the advantages of the DDH-400ZW punch press, new energy automobile companies can produce high-quality, high-efficiency motor stators and rotors, enhance product competitiveness, and develop a broader market share.
To sum up, the DDH-400ZW high-speed precision punch press has an important influence in the new energy automobile industry. By increasing production efficiency, improving product quality, increasing production flexibility, reducing production costs and strengthening market competitiveness, this punch brings huge improvement and development opportunities to the new energy automobile industry and further promotes the development of the new energy automobile industry.
With years of hands-on experience, I have honed my skills in navigating the complexities of global commerce, offering invaluable insights and solutions to address customer needs. My commitment to excellence and dedication to customer satisfaction ensure that I deliver exceptional service, guiding clients through every step of the trading process with confidence and proficiency.